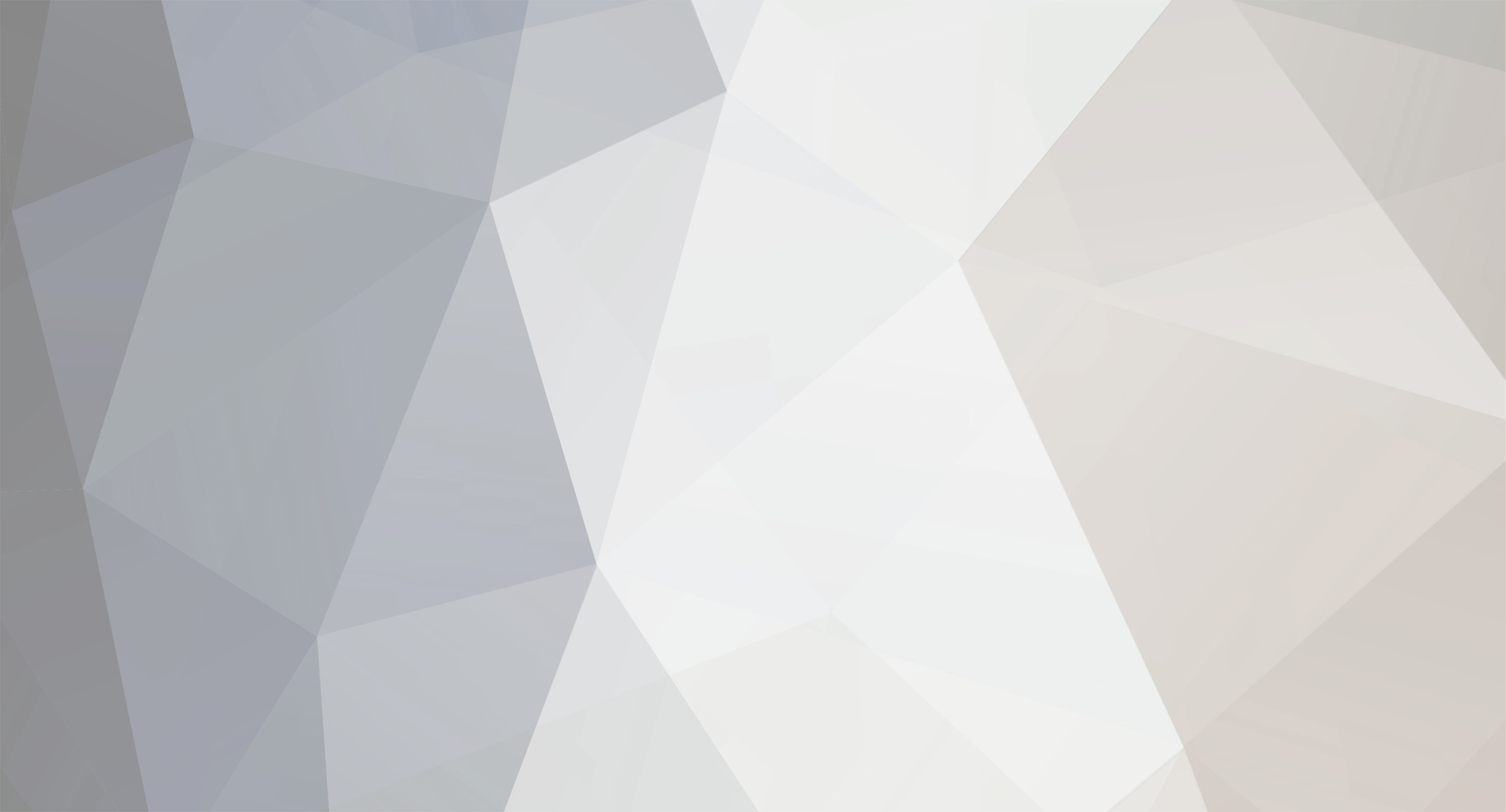
4knflyin
Members-
Posts
130 -
Joined
-
Last visited
Previous Fields
-
Are You Human?
Yes
-
Scale I Build
1/12
Contact Methods
-
Website URL
n/a
-
Yahoo
n/a
-
Skype
n/a
-
Facebook
n/a
Profile Information
-
Full Name
Marcus Girrard
Recent Profile Visitors
The recent visitors block is disabled and is not being shown to other users.
4knflyin's Achievements

MCM Friend (4/6)
-
4knflyin started following Another of the ubiquitous Tamiya 1:24 "Porsche 959" , Tamiya / Top Studio McLaren MP4/6 1/12 , Fujimi Fina McLaren F1 GTR Long Tail and 4 others
-
Fujimi Fina McLaren F1 GTR Long Tail
4knflyin replied to Nacho Z's topic in WIP: Other Racing: Road Racing, Land Speed Racers
Agreed, it is gorgeous! And the way you did those windows, paying heightened attention there, really did pay big dividends. After the yellow Harrods GTR livery, this is my favorite. Yet what do I have in my stash? The attention grabbing, can’t take your eyes off it, Ueno Clinic gray on gray with silvery gray highlights… my least favorite GTR livery. A few months ago, Spot Model erroneously started advertising pre-order for the MFH 1:12 Fina and I added it to my notifications. And then it disappeared… without notification. “Sorry, not sorry.” Great work on this, as usual! -
I do have some questions/comments re: the feedback: Brian, "paint tester body forms." That's a new one on me. I think it's a suggestion I can't afford to pass up. About your painting suggestion, are we talking thin coats allowed hours or days to dry, or just a five-minutes between sort of thing? Laski decals? Misspelled, out of business, or could you give me a link? Thanks. Oh, you have no idea. The only parts removed that didn't fall off are the contents of the equipment bays. Even the engine came loose by itself. Otherwise, I'm working on a completed kit. Worse, the plastic has been uncoated and exposed for 45 years. I'm afraid that if I pry at an important part, I may not have much to work with afterward. Truth. And the plastic is rotted. It took me a good six weeks to realize that the "scratches" showing through the paint and some other "painting defects" were actually the plastic underneath. It's falling apart and cracking. Some pieces I stopped perfecting because the were breaking. Even sanding that ancient bare plastic was a mistake. #600 didn't sand it, it clawed it. And no matter how far I went up the ladder of grits, and no matter how many added layers of primer and paint I through at it, those claw marks still show through. Also, thanks for all your contributions. You're a good read.
-
Hey guys, thanks very much. I just logged on to include a couple photos of other peoples' work on this same kit as a way of maybe getting some feedback... only to find great feedback (though not good news) was already here and the problem was my notifications settings somehow got reset. Again, Thanks! Now that I feel comfortable that I know what can be known about it, my solution after reading your input is to sand just enough to make it sort of passable, avoiding the space between the rivets entirely. Clear coating is a '?." I don't know if I have what it takes to deal with any more coatings on this one. The decanted TS-14 is extremely smooth once attended to, and sometimes right out of the airbrush, so it shouldn't hinder decaling by omitting a coat of clear. The rivets that stand out in the pictures I posted are 0.5 mm lead "solder balls." If you think it's easy to mistakenly damage or destroy a molded rivet with errant sandpaper, try running a sheet across lead rivet. (To do the balls as rivets: I made a tool out of a bamboo toothpick to pick them up and place them. I timed the process, not included drilling the holes, and it took 32 minutes to place 63 solder balls. I figure, including drilling at the locations of the existing molded rivets and the need to make a replacement tool along the way, it's a manageable 2.5 - 4 hrs. Also, the jagged line in front of the emergency access is not an error.) I'm going to include the photos of the other builds. One is from John B. here ("Nacho"), and the other a polish guy. Both are from over a decade ago. The great finish they produce is easier to see on the Polish guys work, the second and third photos. I convinced myself they were carefully sanded and polished, but it may just be my lack of an experience-produced critical eye: It was hard to pick a photo from this guys gallery. I chose this one because it shows the side and tops of the cockpit. In particular, it shows the the tricky area to sand in front of the shifter bump out, and also clearly the rivets on the top of the cockpit. This is a bonus pic. Included because it focuses on the area I focused on in my original post.
-
I really want to put this project to bed. I've been working on refinishing the body/chassis of a Lotus 78 build from decades ago. Not having a method for sanding around the rivets has resulted in costly setbacks because I've had to paint and repaint so many times. I'd like this last repaint to be the last, and that's going to require help. How do you do it? Is it just a matter of getting the the paint down in a with a degree of precision that can pass without sanding? Seeing a couple of other builds of this same kit, Tamiya's 1:12 Lotus 78, and the splendid finishes on them, I hardly think that can be it. This isn't the first time I've wanted to know how to do it. And like all the other times when, whether out of idle curiosity or when I was just a boy building airplane models (when, as I recall, all the rivets were raised) I've wanted to know how to deal with sanding and finishing a model with raised rivets without sanding them out of existence, my searches have come up empty. I'm and I'm afraid I may go to the grave without ever pulling it off 😭 (it's just so sad). A couple of pics of an area of the body that I just last week had to finally replace rivets on because I needed to sand the surface in a way that I couldn't save the originals. I'm hoping the first pic makes clear the need to sand... or whatever it is that I haven't figured out!
-
Great minds think alike? I had already started using ice cold water to rinse between grindings. Decided I would try sticking it in the freezer and holding it against some frozen peas to keep it cold — and hopefully solid — while I worked on it. I couldn't help but notice long ago that just holding thin epoxy resin casting for any length of time transfer enough heat from my fingers to turn it rubbery. When I saw your replies, I decided I needed to try my plan before replying back. So I did it and it was noticeably, but only slightly, better. Mike, I checked out the Createx Clear Acrylic and I'm not sure I understand. You put clear coat in your molds to make castings? Or did you mean to mention this Createx product ($$$): https://sculpturesupply.com/products/epoxacast-690-clear That stuff looks like the ticket. Does anybody have experience with it they want to share with us? For that kind of money (and I haven't even checked on the shipping), it would be nice to have more info, even if it was a vastly different application, before I do an experiment with it. I almost forgot to mention, thanks for turning me on to that website. Thats a lot of stuff they've got going on that could be useful.
-
I could have answered this right away because each time I rinsed it between sanding grits it amazed me how the water spots were crystal clear. I have some Alclad Klear Coat that it says can be used for dipping. I've tested it, but on a part that wasn't representative of something like this. Hopefully to save me some grief, how do you deal with keeping the dipping solution from pooling along the edges? Anybody? Here's some evidence: Held above the water. And submersed (this kind of says it all).
-
I've spent at least two hours over the past two evenings. Last night I started with #600, then #1000 and each whole 1000 until after #9000, where's there's a gap in the sanding sticks I use until #12,000. I started it over again last night and got to #4000, which is where I started tonight. Did the rest of the routine, plus Tamiya Coarse through Finish, and ended with Meguiar's Ultimate. The polishes were applied with a Dremel tool on the lowest setting (which is still pretty fast). The material is Janchun epoxy resin. They practically have a monopoly on Amazon. Importantly, the 'glass' started out perfectly clear straight from the mold. There were two significant "air-holes" that I had to fill, hence the sanding. This is the back window on my 959 build, where nothing, but nothing, comes easy. I hope you can help. (The deep scratches have me scratching my head, but I want to focus on the milkyness.) Here's an example of another part I cast with the same resin on the same day, Monday, I believe. These are pictues of the window starting after #12000 through to Meguiar's. This is after the #12000 sanding: After Tamiya Coarse (about 2 or 3 min. per side): After Fine: After Finish: And finally, an hour later, this is what it looks like now after using Meguiar's Ultimate
-
Another of the ubiquitous Tamiya 1:24 "Porsche 959"
4knflyin replied to 4knflyin's topic in WIP: Model Cars
Thanks for saying that, not just because it's nice, but you are giving me an entrée to feed my ego. I read your 959 thread, and Kurts, too. I wish I had his patience — and skill — to make a couple intercoolers. Now for my starving ego: that engine cover got hours and hours of my attention. With each repainting and the changes to gaps that causes, I maintained my goal with that thing: I added the gap, not by just raising the deck, but by sanding what is actually almost a flat line from where it meats the fender skirt up and over the sharp peak. And more important to me than the gap was maintaining the sheet metal (reinforced fibre, I believe) curves that are complex back there, complex and beautiful. At each stage that I took photos of the car, I always included one showed that unbroken flow. If I you didn't give me an opportunity to tell you about it ad nauseum, nobody would have noticed. Still, not many, if any, will get it. Hah! And the opening under the spoiler. Damn. About 30 sec. of careless sanding in that tunnel resulted in my having changed the shape of the semicircle at either end. Than 30 sec. cost me 10 hrs. or more of body repair work. If anybody knows what the pink polyester putty it is that lots of builders are using, please, please post it here. Thanks. Now I'm going to show you stuff that only I think warrants this much attention! It started out innocently enough. Just a bit of light sanding since I was repainting it anyways. Then started big investment of pride in the outcome. Not to mention the big investment of time in "care and feeding" of the beast. Subtle use of Tamiya epoxy putty, which I found oddly soothing to maticulassly feather it to blend with the body. But fixing that 30 sec. of damage to the tunnel, that was not soothing, relaxing, or anything else pleasant. Many very frustrating hours into it, I figured I just wasn't going to be able effectively sand in those corners. And then a eureka moment that lead to results way better than I was expecting, though leaving lots of room for justified criticism from the highly skilled. What you saw there took a long time to do. Tens of hours in all tolled, I'm pretty sure, on just the engine cover/spoiler/fender meeting point. Mathias, you almost certainly get it. It has beautiful lines. -
Another of the ubiquitous Tamiya 1:24 "Porsche 959"
4knflyin replied to 4knflyin's topic in WIP: Model Cars
Great screen name, m’lord. Wow, John, you’ve got a great memory, especially for someone who hasn’t even built the kit. Yes, I’ve read the stories. We shall see! -
Another of the ubiquitous Tamiya 1:24 "Porsche 959"
4knflyin replied to 4knflyin's topic in WIP: Model Cars
So, I buried the lead on this post when I first submitted it. This experience is what cemented in my mind that I am not seeing details normally. I’m basically not seeing fully stereoscopically. The paint job, that I'm not all that unhappy with, went through three cycles of prime, paint, varnish. Three cycles without ever stripping it. LOL. I won't do that again. As I was advised on an earlier model, just strip it down. It wasn't my plan each time to do a complete cycle, it just ended up after failing at spot repairs and so forth that I just sprayed the whole thing with primer to hide the mess. #1 - Somehow I missed that I hadn't completely erased the parting lines until I'd primed it the second time. So I had to do this. What you see on the fender is primer on top of silver gray on top of primer. And in the middle of it all is putty because I had wrecked the shape of the fender. #2 - After putting a coat of the color down, I still hadn't erased the lines. This is the vision thing. It sucks. What really helped me decide to repaint it was that the engine cover looked noticeably different than the bulk of the body. The two remaining cycles of painting were done with the cover on the car so I could know it was getting exactly the same treatment as the rest of the body. #3 - The primer always looked awesome. Very tempting. Why doesn't it look as tight as the test spoon? Spoon has only one coat of color coat! And, more importantly, I still haven't noticed the lip of paint that had collected over three cycles of painting, that had collected at the top of the rear window opening. Still #3, the final major repaint. What the photo doesn't quite show is that the gloss coat is satiny smooth, like the "frozen" colors way too popular these days. Now I'm on to the lip. It has to go. That scratch in the paint? I told myself before I repainted the roof that it would be the end of chasing perfection for the paint job. And I stuck to it. So it stays, preserved under gloss. Removed the tap covering the grill opening and also removed some paint I wanted to stay put. The only solution I could think of was putty. It worked great. Totally unnoticeable. From the tape I removed I was able to measure how thick the three cycles of painting was: 0.12 mm. That probably only sounds thick to somebody who knows paint. I was finally comfortable that it had seen it last repainting, so I was also comfortable enough to paint the trim. I'm often curious how other people tape off for painting. This is the final product, as it is today. The headlamps are a mess. Three complete paintjobs piled on top of each other. And my only regret, besides the headlamp bezels, is that I stopped at two coats of color. The roof, which has a fourth coat, has a much tighter grain. -
Another of the ubiquitous Tamiya 1:24 "Porsche 959"
4knflyin replied to 4knflyin's topic in WIP: Model Cars
An inauspicious start: I was so tired of reworking the F1 models I started my return to the hobby with, that I pulled out the last of the purchases from 1994, this 959, because I just wanted to look at it. I literally thought to myself how nice it was going to be to start with a clean sheet. A fly landed and, not something I usually do, I swatted at it. It was on the other side of the 959 shell on my desk. The underside of my forearm came down on the roof of the car and, before I even intended to start on it, I broke the B and C pillars at their tops, and creased the A pillar. You will see in various photos the size of the B pillar grow in girth from more than five repairs. Then, finally, I scraped it down and did it right. Amazingly, the bottom part of it never separated from the door. That was 2 June, for reference. -
Another of the ubiquitous Tamiya 1:24 "Porsche 959"
4knflyin replied to 4knflyin's topic in WIP: Model Cars
This is where I'm at now, and have been for over a month. I think what I'm going to do is just show the progression of certain parts, which is a lot of build, break, rebuild worse, etc. If anybody wants an explanation beyond any I provide, please ask, I'm eager to respond. Observations/suggestions (other than find a new hobby), really, please, make them. The current state: Actually, I'm going to show you the only thing that worked right away and that was satisfying way beyond it's utility. I couldn't stand picking up the chassis and having the front wheels flopping around. The unhinged right rear, I could deal with that. But the fronts really bugged me. The very effective solution: 2.4 mm of 1.7x1.5 brass tube. Press fit. That's all it took to give me a tight front end and great satisfaction. However, even here, if you noticed the two tiny holes in the subframe, they're the ends of 0.5 mm SS rod that's supporting the standoffs on the other side that I broke off. I'll bet nobody else has found a way to break those off. And so it begins, the lasting legacy of this build: repair, repair, repair. I still turn the wheels left and right every time I see the chassis. Very satisfying. -
It seems it could be a sort of right of passage. It's my first passenger car. The greatest significance of that is that it has an interior. That's like another skill set all together. I tried adding to the interior by getting the Quinta 3D decal set. Very conservatively, the work so far has be split 25:70:5, build:repair:naval-gaze. In all honesty, the repair portion is likely bigger. I'm not sure I can sustain that. I'm going to try to build least two more kits and see if I can find it rewarding to build at what I think I now know is my skill level. If not, the rest of my kits may be on the market done in a year or so. Why?... I'm not aging gracefully as I had always expected (gym rat, good food, etc.). To add to the unsteady hands I noticed when I started back at this hobby a year ago, I also could swear that I wasn't able to make detailed visual distinctions and judgements very well. I have to take a picture of anything I want to know if it's correctly done, which gets annoying and not done as often as I should. The short of it: I finally went to an ophthalmologist a couple weeks ago and, no, I wasn't imagining it. Options aren't great, so for now I see how it goes. The moral of the story is, if you're still under, say, 65 and putting off building that model you've been thinking about, maybe now is a good time to start it. Back to my right of passage. I bought the kit a year after Porsche stopped producing the car, 1994. Hand painted some parts on the sprue, actually glued three pieces together (that's them falling out of the bonnet, or mating with the box, I'm not sure), and that was it until last fall.
-
Model factory hiro Porsche 935/78
4knflyin replied to Brudda's topic in WIP: Other Racing: Road Racing, Land Speed Racers
I'd love to think I helped. lol. Also, I just noticed the rear wheel arch... it's rounded like your friend suggested, but certainly rounder than he was envisioning. IIRC, symmetry with the front arch was what he was suggesting, an idea I immediately liked. I think it's true that certain design concepts are universally pleasing to the eye, and symmetry is chief among them. This is a great build to watch. Wishing you heaps of "mojo" 'til the end.